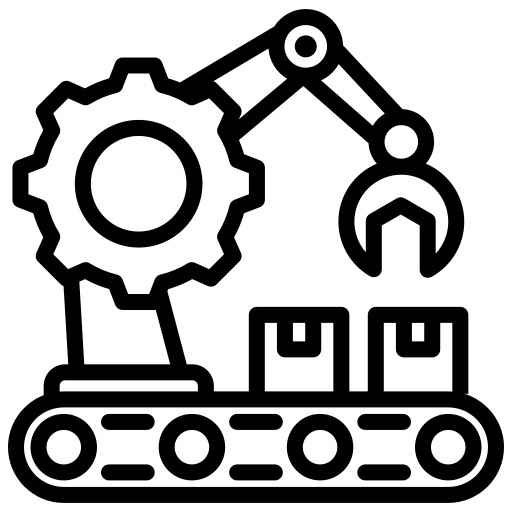
Description
This project aims to redesign and improve an existing (X,Y, (Z)) gantry robot to reduce costs and enhance its performance, with focusing on that fact that the standard dimensions in the existing gantries, are not changeable. The process involves studying the current robot, creating detailed 3D models, and exploring alternative components to optimize its design. The ultimate goal is to deliver a solution that is affordable, dimensions adaptable, and ready for practical use across various applications, all while ensuring thorough documentation for future use.
The project focuses on three key objectives. First, reducing costs by identifying affordable yet reliable components. Second, enhancing the robot’s performance to meet modern industrial needs. Third, providing clear documentation to simplify replication and deployment.
Why This System is Needed
Gantry robots play a vital role in industries like assembly, transportation, and precision manufacturing, where efficiency and cost-effectiveness are critical. However, existing solutions often have significant limitations:
- High Costs: Even big companies are using standard affordable components, their final price remains important.
- Limited Optimization: Current systems struggle to adapt to specialized needs, such as cleanroom or biomedical environments.
- Lack of Scalability: Most existing gantry robots aren’t flexible enough to accommodate varying design dimensions and sizes, making it difficult for companies to customize them for industry-specific machinery without significant investments.
This project addresses these challenges by creating a more affordable, versatile, and well-documented gantry robot that supports a wide range of industrial applications.
How We Plan to Achieve It
The project will be implemented in four phases, each with a clear focus:
1. Analysis of the Existing Gantry-Robot
- Study its mechanical and electrical components. Also, analyzing the market prices.
- Sample key parts to assess their strengths, weaknesses, and areas needing improvement.
- Use software like SolidWorks to create a precise 3D model, providing a foundation for the redesign.
2. Robot Improvement
- Identify specific design aspects to improve, such as functionality, reliability, and cost-efficiency. Consider this that after researching the used components to improve, we should be able to get these components from trustful and reliable suppliers.
- Research and test alternative components that are more affordable while maintaining quality.
- Explore materials suited to different environments, such as cleanrooms, biomedical settings, or those requiring UVC resistance.
- Completely new ideas of how the gantry new generation could be.
- First concepts trade-off.
3. Prototyping and Testing
- CAD Tools & Documentation: Utilize SolidWorks as the primary CAD platform while exploring economical alternatives such as FreeCAD or other student-licensed programs, ensuring delivery of final 2D PDF files and preserving SolidWorks 3D models for traceability.
- Design & Adaptation: Develop parameter-guided 3D models to enable size adaptation and gain familiarity with the company’s 3D model organization and Product Data Management system.
- Prototype & Validation: Build a prototype incorporating the proposed improvements and conduct thorough testing to verify performance, reliability, and adaptability standards.
4. Documentation
- Create detailed project documentation, including assembly instructions and testing results.
- Prepare test reports and a comprehensive manual to support deployment, replication, and scalability.
This step-by-step plan ensures the project is executed systematically, with each phase building on the previous one to achieve the best results.
Project Timeline
- Phase 1: Analysis – 40–60 hours
- Phase 2: Redesign and Optimization –100-120 hours
- Phase 3: Prototyping and Testing – 70-90 hours
- Phase 4: Documentation and Evaluation – 40–50 hours
Total Time Frame: 250–320 hours